Fabrication de circuits imprimés
Tous les PCB et stencils de Formatronic sont fabriqués dans nos usines de Pingxiang et de Huizhou qui emploient 700 personnes et fonctionnent 24 heures sur 24 en équipe de 8 heures avec une capacité de production quotidienne de 10 000 m2.
Homologuées UL, certifiées ISO 9001, ISO 14001, ITAF 16949 (Automobile), EN 9100 (Aéronautique) et ISO 13485 (Médical) , implantées dans la plus grande zone de fabrication de PCB au monde, les usines offrent une réactivité optimale notamment grâce à des relations privilégiées avec leurs fournisseurs (laminés, encres, produits chimiques).
Elles disposent notamment de son propre stock de matières premières (KingBoard, Shengyi, HITEK, Rogers) ainsi que d’un stock physique permanent chez nos partenaires.
2 lignes de production dont une entièrement dédiée à la fabrication des prototypes de circuits imprimés en délai express nous permettent de satisfaire au triptyque qualité, prix et délai selon les normes en vigueur.
Un personnel hautement qualifié associé à un équipement ultra moderne sont les garants d’une fabrication irréprochable notamment pour les circuits imprimés qui requièrent des classes de gravure particulièrement fines (isolement minimum 0,075 mm sur cuivre de 12 à 18 µm et 0,1 mm sur cuivre de 35 µm) ainsi que pour les pcb HDI (via laser, empilage spécifique).
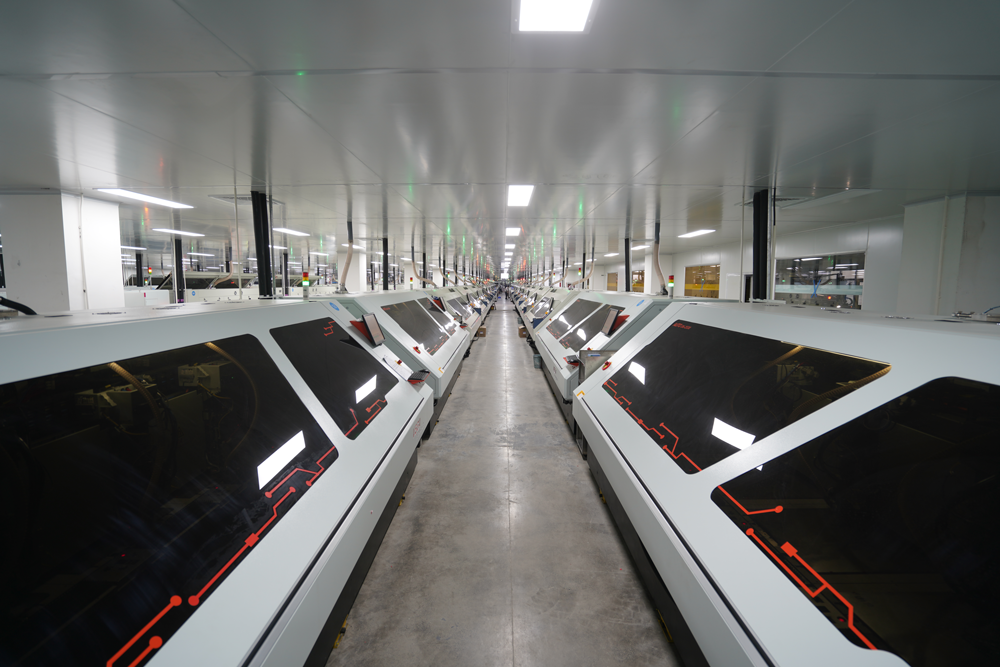
Circuits imprimés rigides
Un circuit imprimé rigide (en anglais printed circuit board ou PCB) est une plaque fabriquée à partir de matériaux composites en général de verre époxy appelé également FR4 (abréviation anglaise de flame retardant 4) doublée avec une ou plusieurs couches de cuivre. L’ensemble peut avoir une épaisseur de substrat comprise entre 0,2 mm et 4,5 mm et une épaisseur de cuivre qui varie de 17,5 µm à 420 µm.
Circuits aluminium - SMI
Appelé également circuit imprimé aluminium, le SMI (abréviation signifiant « substrat métallique isolé ») est un PCB fabriqué sur une plaque métallique, en général en aluminium, qui se présente sous la forme d’un circuit imprimé simple face ou double face dont l’épaisseur de substrat et de cuivre peut
varier selon les projets. Le principal avantage du SMI est de dissiper la chaleur de certains composants notamment les LEDs.
Circuits imprimés flexibles
Un circuit imprimé flexible est un PCB qui a la capacité physique de se plier, fabriqué à base de polyimide (PI) qui se caractérise par une résistance élevée aux manipulations physiques et à la température, il bénéficie d’un revêtement protecteur en coverlay. Disponible en simple face, double face et multicouche (jusqu’à 12 couches), le circuit imprimé flexible a une épaisseur minimum de 0,05 mm.
Circuits imprimés flex-rigides
Un circuit imprimé flex-rigide est un assemblage de parties rigides reliées à des parties flexibles interconnectées. Ce circuit imprimé de type hybride est disponible jusqu’à 30 couches.
Capacités de production
Circuits imprimés rigides |
Nombre de couches |
1-34 couches |
Nombre de couches (boutique en ligne) |
1-12 couches |
Largeur minimum de piste |
3 mils – Epaisseur du cuivre fini 25 µm |
Diamètre de perçage minimum : |
Epaisseur circuit imprimé ≤ 1.2 mm |
0,15 mm – diamètre de perçage |
Epaisseur circuit imprimé ≤ 2.5 mm |
0,20 mm – diamètre de perçage |
Epaisseur circuit imprimé > 2.5 mm |
Ratio aspect ≤ 13:1 – diamètre de perçage |
Dimension maximum panneau |
610 x 1100 mm |
Epaisseur du circuit imprimé fini : |
Epaisseur maximum |
4.2 mm |
Min. 2 couches |
0.2 mm |
Min. 4 couches |
0.4 mm |
Min. 6 couches |
0.8 mm |
Tolérance d’impédance |
± 10% |
Traitement de surface |
HAL sans plomb, Ni / Au chimique, argent chimique, OSP, Hard gold, Pelable, Carbone. |
Principaux fournisseurs de laminés |
Shengyi, Isola, Iteq, Arlon, Rogers, Taconic, Nelco, Wangling, Kingboard. |
Circuits imprimés flexibles et flex-rigides |
Nombre de couches circuits imprimés flexibles |
1-8 couches |
Nombre de couches circuits imprimés flex-rigides |
Jusqu’à 12 couches |
Isolement minimum |
12&18µm (Cu de base):0.075/0.075mm; 35µm (Cu de base):0.1/0.1mm |
Raidisseur |
Polyimide FR4, PSA, métal, ou selon demande client |
Circuits imprimés multicouches + Flex |
Assemblage pour construction multicouche |
Tolérances d’outillage : |
Outil de poinçonnage |
± 0.25mm |
Outil de précision |
± 0.05mm |
CNC perçage / routage |
± 0,10 mm |
Traitement de surface |
HAL sans plomb, Sn/Pb, Ni/Au chimique, Or électrolytique, soft/hard gold, argent chimique, OSP |
Maximum de couche à couche |
± 0,10 mm |
Epaisseur de métallisation (pour trous métallisés) |
8~15µm;20~30µm;30~70µm (spécial) |
Epaisseur d’or |
Ni/Au Ni : 2~6µm; Au : 0.035~0.075µm; soft/ hard gold Ni : 2~9µm; Au : 0.035~0.1µm |
Impédance
Les impédances contrôlées des pistes de pcb.
L'impédance se mesure en Ohms et elle permet de mesurer la qualité de la gravure des pistes. l'impédance est une caractéristique en courant alternative (AC) qui augmente avec la fréquence et devient critique pour les circuits imprimés fonctionnant à des fréquences supérieures à 200 ou 300 Mhz.
Le logiciel de calcul d'impédance est un bon point de départ pour déterminer la largeur (w) de piste et l'épaisseur (h) de l'isolant d'une impédance spécifique. S'agissant du trafic de signaux dans les circuits imprimés, lorsque des pistes transmettent des signaux à hautes fréquences, un très grand soin doit être apporté à la conception des pistes pour adapter l'impédance à celle des composants situés en amont et en aval. Plus la piste est longue ou la fréquence élevée et plus l'adaptation est nécessaire. Le fabricant de circuits imprimés va contrôler l'impédance en agissant sur les dimensions et et espacements de la piste et de l'isolant. Quand on regarde les empilements d'un circuit multicouches,
il faut se souvenir que les pistes internes à impédance contrôlée sont blindées par des plans et pour cette raison, il ne faut prendre en compte que l'épaisseur d'isolant entre les plans de part et d'autre de la piste, si elle est interne au PCB.
Fabrication des circuits à impédance contrôlée.
La vitesse de fonctionnement des composants électroniques augmentant, le besoin de PCBs à impédance contrôlée augmente lui aussi.
Si l'impédance est incorrecte, il est difficile d'identifier le le problème une fois la carte câblée. Puisque l'impédance dépend de nombreux paramètres (largeur et épaisseur de piste, épaisseur du stratifié,
etc...), FORMATRONIC teste 100% des circuits imprimés à impédance contrôlée. Le test n'est pas fait sur le circuit imprimé lui-même, mais sur un coupon de test du même panneau et fabriqué en même temps.
Le coupon de test typique est un circuit imprimé qui a les mêmes caractéristiques et empilages que le circuit principal. Ses pistes à impédance contrôlée ont les mêmes dimensions que celles du PCB et sont dans les mêmes couches.
Les indications suivantes vous donneront une idée des relations qui existent entre valeur d'impédance et dimensions, il faut se souvenir qu'il s'agit seulement d'approximations dans le cas des pistes fines.
• L'impédance est inversement proportionnelle à la largeur de piste.
• L'impédance est inversement proportionnelle à l'épaisseur de piste.
• L'impédance est proportionnelle à l'épaisseur du diélectrique.
• L'impédance est inversement proportionnelle à la racine carrée de Er du diélectrique.
Pour toute information, n’hésitez pas à nous contacter par e-mail contact@formatronic.eu pour plus d’information. Nous nous ferons un plaisir de vous répondre.
Préconisation de stockage et de conservation des circuits imprimés

1 – Lieu de stockage conseillé : pièce climatisée ou armoire climatique, appelée également armoire de stockage au sec.
Une armoire de stockage au sec permet de stocker en atmosphère sèche des composants électroniques, des cartes de circuits imprimés équipées et nues ainsi que des produits semi-finis qui sont sensibles à l’humidité. Cela empêche la pénétration de l’humidité dans les composants et que ces derniers soient endommagés pendant le brasage. Il est possible de remplir l’armoire de stockage au sec d’air comprimé et/ou d’azote en fonction du niveau d’humidité nécessaire pour créer une atmosphère faiblement humide. Si ils ne sont pas stockés dans des conditions optimum, T° = 22°c ± 3°c et Humidité = 50% ± 10 %, nous préconisons de les repasser en étuve en cycle court à 150°c durant 2 heures ou en cycle long à 50°c durant 8 heures.
2 – Nécessité du stockage en atmosphère sèche.
L’humidité provoque des dommages : les composants, les produits semi-finis et les cartes de circuits imprimés sont sensibles à l’humidité. S’ils sont stockés dans des conditions ambiantes normales, l’humidité présente dans l’air peut s’y infiltrer. Les composants sont exposés à des températures élevées pendant les opérations de brasage durant lesquelles cette humidité s’évapore et produit de la vapeur d’eau. Celle-ci se dilate exerce une forte pression sur les composants. La vapeur d’eau se dégage soudainement provoquant alors des dommages irréversibles si la charge limite de pression est atteinte.
Directive RoHS : depuis le 1er juillet 2006 conformément à la directive CE 2002/95/CE certaines substances qui étaient jusque-là utilisées dans la fabrication de composants électroniques sont désormais interdites. La directive dite RoHS (Restriction of the use of certain Hazardous Substances) sur la limitation des substances dangereuses dans les équipements électriques et électroniques prévoit, entre autres, la soudure sans plomb des composants électroniques. Les métaux de brasage au point de fusion plus élevé qui remplacent désormais les alliages contenant du plomb nécessitent des températures plus élevées à la soudure. Ces températures plus élevées augmentent les contraintes exercées sur les composants, les produits semi-fini et cartes de circuits imprimés pendant la soudure et peuvent entraîner des dommages.
Taille des composants : La tendance à la miniaturisation des composants ne cesse de s’affirmer. Les composants deviennent de plus en plus petits et nécessitent de moins en moins de place. Cet espace réduit doit, en même temps, abriter toujours plus de fonctionnalité. Cela rend les composants de plus en plus sensibles à l’action des conditions ambiantes. Droit à la garantie : Les fabricants et négociants de composants et de cartes de circuits imprimés indiquent dans quelles conditions il convient de stocker les composants électroniques. La garantie s’éteint s’ils sont stockés dans des conditions ambiantes non appropriées.
3 – Ce que l’on doit stocker.
Les composants : Les composants doivent être stockés dans une atmosphère sèche selon les indications des fabricants. Ces composants sont emballés en sachet sous vide. Si tous les composants d’un lot ne sont pas utilisés pour équiper un circuit imprimé, les éléments restants sont stockés dans une armoire de stockage au sec. Pcbs et produits semi finis : Les circuits imprimés doivent être utilisé autant que possible dans une atmosphère sèche. Ils pourraient sinon absorber de l’humidité ce qui peut entraîner des dommages durant la soudure. Il faudrait stocker aussi bien les PCBs nus avant soudure que les cartes équipées, en totalité ou partiellement, dans une armoire de stockage au sec. Cartes équipées : Les cartes équipées ne sont pas toujours utilisées immédiatement, mais étant donné que celles-ci sont sensibles à l’humidité, tout comme les différents composants, un stockage dans une armoire de stockage au sec s’impose.
4 – Conséquences dues à un mauvais stockage.
L’effet « Pop-Corn » : L’humidité présente dans l’air ambiant peut, dans des conditions ambiantes normales, pénétrer dans les composants électroniques et les circuits imprimés. De la vapeur d’eau se forme à l’intérieur de ces composants dès qu’ils sont exposés aux températures élevées dégagées lors des opérations de soudure. Cette vapeur d’eau produit une forte pression qui fait éclater les composants électroniques et les circuits imprimés. Cet éclatement dit « effet pop-corn » entraîne des dommages irréparables tels que le décollement inter-laminaire ou des microfissures.
Décollement des couches : Les composants électroniques et les circuits imprimés sont souvent constitués de plusieurs couches de matériaux. La pression qui se produit pendant la soudure en raison de la vapeur d’eau sépare les différentes couches et entraîne ainsi une instabilité. Ce phénomène est issu de l’effet « pop-corn » et est qualifié de « décollement inter-laminaire ».
Microfissures : L’effet « pop-corn » entraîne également des microfissures. La vapeur d’eau qui s’échappe des composants électroniques ou des cartes de circuits imprimés pendant la soudure produit des petites fissures microscopiques qui les rendent inutilisables.
Dommages dus à l’oxydation : Lorsque les circuits imprimés sont stockées dans des conditions normales, l’oxygène présent dans l’air ambiant entraîne l’oxydation de la couche en étain qui recouvre le matériau de base. Il était jusqu’alors possible de compenser l’oxydation minime par la fluidité des alliages d’apport contenant du plomb. Les alliages d’apport sans plomb posent, par contre, des problèmes en mouillant la surface et ne sont pas suffisamment agressifs. Cela entraîne des défauts de soudure tels que des points de soudure pas assez mouillés et donc des composants qui bougent.
Eclatement et retassures : La vapeur d’eau qui se produit pendant l’opération de soudure s’échappe soudainement des composants électroniques. Elle entraîne, outre le décollement laminaire, également des éclatements et des retassures internes. Les éclatements se produisent lorsque la vapeur d’eau s’échappe des points de soudure et provoquent alors des trous. En ce qui concerne les retassures internes, la vapeur d’eau reste dans le matériau des composants. Cela entraîne la création de cavités remplies de vapeur d’eau qui rendent les composants électroniques instables et donc inutilisables.
5 – Stockage à long terme.
Dommages dus à l’humidité et à l’oxydation : Si les composants ou Cartes étaient stockés à l’air ambiant normal, ils absorberaient l’humidité présente dans l’air et deviendraient inutilisables peu de temps après. Les surfaces métalliques s’oxyderaient en raison de l’oxygène présent dans l’air ambiant. Etant donné que les composants ou cartes doivent être vendus comme des éléments neufs même après des années, un stockage adéquat doit garantir l’état d’origine de ces éléments.
Stockage dans l’azote : une atmosphère composée d’azote, comme c’est par exemple le cas dans une armoire de stockage au sec, convient au stockage à long terme pour des composants, des circuits et des cartes. Cet environnement sans oxygène empêche la pénétration d’humidité et l’oxydation des surfaces métalliques ce qui permet de conserver l’état d’origine des composants et des modules. Cela permet de les utiliser sans problème même après de longues années de stockage.
6 – Avantages du stockage au sec.
Différentes méthodes de séchage : Différentes méthodes de séchage ont été mises au point pour pouvoir utiliser des composants, cartes et circuits imprimés. Il est ainsi possible de « cuire » des composants électroniques, par exemple avant leur utilisation, dans une étuve. Il est en plus possible de remettre en stock les composants non utilisés dans des sachets sous vide. Une troisième méthode consiste au niveau du stockage des composants, cartes ou circuits imprimés à les associer à des sachets de billes de silice qui absorbent l’humidité présente dans l’air et les composants. L’armoire de stockage au sec qui fonctionne avec de l’air comprimé et de l’azote est la solution qui présente les meilleurs avantages par rapport à toutes les méthodes mentionnées ci-dessus.
Séchage par cuisson : La cuisson des composants, cartes et circuits imprimés nécessite de fortes dépenses logistiques. La cuisson peut durer entre plusieurs heures et jusqu’à quatre-vingt jours en fonction de la température et de l’épaisseur des composants. Les températures élevées exposent, en outre, les composants électroniques à d’importantes sollicitations structurelles. La cuisson est synonyme d’une consommation énergétique très élevée tandis que celle d’une armoire de stockage au sec est, par comparaison, faible. Une armoire de stockage au sec permet également de retirer les composants justes avant de les utiliser sans avoir besoin de les préparer longuement. Ils ne sont pas exposés aux diverses contraintes pendant le stockage.
Emballage sous vide : les composants, cartes et circuits imprimés sont emballés dans des sachets sous vide neufs, les « Dry-Packs » qui seront ensuite soudés. Les « Dry-Packs » nécessitent à chaque fois une nouvelle étiquette (ce qui n’est pas le cas pour l’armoire de stockage au sec) si bien que cette méthode prend également beaucoup de temps. Cette méthode n’implique également pas un reséchage actif, ce qui signifie que l’humidité qui s’est infiltrée dans les composants, les cartes et les circuits imprimés y reste et risque de poser des problèmes lors de leur utilisation ultérieure.
Emballage avec sachet de silice : les composants, cartes ou circuits imprimés sont stockés dans des récipients appropriés contenant des sachets de silice. Les granulés ou les gels absorbent l’humidité de l’air et des composants et renvoient cette humidité à l’air extérieur dans un processus adapté.
Formatronic, spécialiste européen de la production de circuits imprimés rigides, de circuits imprimés rigides, de circuits imprimés flexibles, de circuits imprimés flex rigides. Fabrication de série récurrente, de prototype pcb, fabrication de série limitée, prix compétitifs de circuits imprimés sur des délais courts.
Tolérances mécaniques des circuits imprimés
Tolérances d'usinage du contour extérieur et des perçages des PCB.
Les tolérances DIN 7168 moyennes s'appliquent.
Tolérances admises par dimensions :
Sans tolérance en mm Extrait DIN 7168 |
Plage de dimensions nominales (mm) sans tolérances |
Précision |
de 0.5 à 3 |
de 3 à 6 |
de 6 à 30 |
de 30 à 120 |
de 120 à 315 |
de 315 à 1000 |
de 1000 à 2000 |
Fine |
+ 0.05 |
+ 0.05 |
+ 0.1 |
+ 0.15 |
+ 0.2 |
+ 0.3 |
+ 0.5 |
Moyenne |
+ 0.1 |
+ 0.1 |
+ 0.2 |
+ 0.3 |
+ 0.5 |
+ 0.8 |
+ 1.2 |
Grossière |
- |
+ 0.2 |
+ 0.5 |
+ 0.8 |
+ 1.2 |
+ 2.0 |
+ 3.0 |
Très grossière |
- |
+ 0.5 |
+ 1.0 |
+ 1.5 |
+ 2.0 |
+ 3.0 |
+ 4.0 |
Tolérances des diamètres :
Trous non-métallisés :
Pour les trous non-métallisés, il faut distinguer les perçages de positionnement, les perçages pour automates de montage des éléments et pour les testeurs, les perçages à tolérances serrées et les perçages de fixation pour le montage du circuit imprimée et des éléments à tolérances normales.
Les trous de positionnement ont leurs côtes inscrites de façon particulière et doivent être percés en même temps que les trous métallisés.
Pour tous les autres trous non métallisés et pas spécialement marqués, les tolérances DIN 7168 moyennes s'appliquent.
Trous métallisés :
Si rien d'autre n'est précisé dans les documents de la commande, les tolérances suivantes s'appliquent :
D < 0,8 mm |
Tolérance : D -0,05 / +0,1mm |
0,8 <= D <= 2,0 mm |
Tolérance : D -0,05 / +0,1mm |
D < 2,0 mm |
Tolérance : D -0,05 / +0,1mm |
D : diamètre final du trou métallisé.
Lors du choix du diamètre, il faut faire attention à choisir les pastilles de soudure correspondantes afin que la collerette restante soit suffisante.
Exemple : Si vous avez besoin d'un diamètre final de 0.8mm, nous devons tenir compte de la métallisation lors du perçage (voir figure). En règle générale, on calcule un supplément de 0.15 mm, c.-à-d. que le trou sera percé à 0.95 mm. Après dépôt des couches galvaniques, on obtient un diamètre final de 0.85 mm environ.
Un exemple à ne pas suivre : pastille de soudure de 0.5mm avec un diamètre du trou de 0.4mm. Si l'on calcule comme ci-dessus un supplément de 0.15 mm, il ne reste plus sur la carte percée qu'une collerette résiduelle constituée par la métallisation du trou.
Tolérances des rainures :
Si les contours des circuits imprimés sont rainurés, les tolérances données ci-dessous s'appliquent.
1. Epaisseur du circuit imprimé 1,0 mm (cartes CMS).
Angle d'entaille V
|
30°
45°
60°
90° |
Epaisseur de lame centrale K |
0,3 + 0,1 mm |
Déport F* de chaque rainure |
+ 0,025 mm |
Déport P* du contour
(après la séparation des circuits imprimés) |
+ 0,15 mm |
* par rapport à la ligne médiane nominale.
2. Epaisseur du circuit imprimé 1,5 mm (cartes CMS mixtes).
Angle d'entaille V |
30°
45°
60°
90° |
Epaisseur de lame centrale K |
0,4 + 0,1 mm |
Déport F* de chaque rainure |
+ 0,025 mm |
Déport P* du contour
(après la séparation des circuits imprimés) |
+ 0,15 mm |
* par rapport à la ligne médiane nominale.
Distance entre les pistes et la ligne de rainurage :
Epaisseur du circuit 0.80 mm : Xmin = 0.3 mm.
Epaisseur du circuit 1.00 mm : Xmin = 0.4 mm.
Epaisseur du circuit 1.50 mm : Xmin = 0.5 mm.
Normes et conditions des circuits imprimés
Fabrication circuits imprimés, PCB, UL, RoHS, REACH, fabrication IPC-A600-2, PCB IPC-1603, pour l’électronique médicale et les marchés militaires
Normes UL, RoHS, REACH, IPCA602/A603.
UL.
Ceci certifie que tous les circuits imprimés en 1 ou 2 couches, de type ES-01, ED-01, ainsi que les circuits multicouches ont été étudiés par Underwriters Laboratories Inc. conformément à la norme UL.
Norme de sécurité : UL 796 – Circuit imprimé – CSA-C22.2 N° 0.17 – évaluation de la propriété du matériau polymère.
Classification : UL 94V-0 (classification générale pour les circuits imprimés).
RoHS.
Restriction of Hazardous Substances.
Ceci certifie que tout ou partie des produits que nous fournissons sont conformes aux requêtes de la Directive (EU) 2015/863 relative à l’utilisation de substances hasardeuses dans l’électronique et les équipements électroniques. La liste suivante correspond aux restrictions sur certains matériaux et à leur limite respective admissible :
Cadmium and its compounds < 100 ppm.
Mercury and its compounds < 1000 ppm.
Hexavalent chromium and its compounds < 1000 pm.
Lead and its compounds < 1000 ppm.
Polybrominated biphenyls (PBB) < 1000 ppm.
HBCDD < 1000 ppm.
DEHP < 1000 ppm.
BBP < 1000 ppm.
DBP < 1000 ppm.
REACH.
Formatronic confirme et garantit que tous les produits livrés correspondent aux règlements REACH et ne libèrent aucune substance.
Formatronic n’est pas soumis à l’inscription et à la création d’une fiche de sécurité.
Formatronic vous informera immédiatement, selon l’article 33 du code REACH, de toute substance considérée alarmante par L’ECHA (European Agency for Chemicals). Actuellement, nous ne prévoyons pas une telle incidence sur nos produits.
Indépendamment de ce fait, nous poursuivons activement la tenue à la règlementation REACH ; nous voulons être garants de cette législation dans notre propre intérêt et pour garantir celui de nos clients. Nous sommes en collaboration étroite avec les différents intervenants du département chimie de nos lignes de productions afin de suivre rigoureusement le processus de qualification respectant la règlementation REACH.
IPCA602/A603.
Ceci certifie que les tous les circuits sont fabriqués selon la norme IPC. La norme IPC est le cadre relatif à la fabrication des circuits imprimés. Les circuits imprimés sont fabriqués selon la norme IPC2 exception faite d'un cahier des charges spécifique à une exigence supérieure telle que l'IPC3. Seule la liste déterminée par la norme IPC peut-être prise en compte pour les éventuels défauts. Les exigences en dehors de ce cadre seront étudiées et ne pourront en aucun cas outrepasser la dite norme.
La liste des défauts non acceptables par l’IPC2 et l’IPC3 sont identiques. La différence est le fait que pour l’IPC2, il est autorisé de retoucher ces défauts alors que cela est strictement interdit pour l’IPC3.
Période de garantie des pcbs.
Finition HAL sans plomb : 1 an.
Finition Nickel or : 6 mois.
Finition OSP : 3 mois.
Finition Argent : 6 mois.
Finition Etain : 6 mois.
La période de garantie est effective à partir du date code indiqué sur le circuit imprimé. Si le stockage des circuits dépasse 90 jours, nous vous conseillons de les étuver en cycle court durant 2 heures à 150°C ou en cycle long à 50°C durant 8 heures. Le stockage adéquat pour la conservation des pcbs en stock est une armoire de stockage au sec qui contrôle la température et le taux d'humidité. Les conditions de stockage optimum sont une T° = 22°c ± 3°c et un taux d'Humidité = 50% ± 10 %.
Introduction aux normes IPC.
La norme IPC est là pour vous aider à construire une démarche qualité rigoureuse sur la totalité de votre chaine de production afin de présenter un produit de haute fiabilité.
Différentes normes sont là pour vous accompagner depuis l’étude de votre produit jusqu’à sa livraison. Les intervenants de l’industrie électronique parlant le même langage, cela simplifie la communication et la compréhension par rapport aux exigences de travail demandées.